AI-powered Management for Defense Drone Swarms Drones are now a...
Read MoreHow AI Transforms Predictive Maintenance in Defense Equipment
Table of Contents
ToggleIn a rapidly changing geopolitical context, artificial intelligence (AI) has firmly established itself as a cornerstone for demonstrating superiority, from threat detection to drone autonomy and cyberattack mitigation.
Yet, one critical area often overlooked in the broader discussion of AI’s impact on defense is predictive maintenance. Despite being central to the effectiveness of military strategies and operations, the immense potential of leveraging vast amounts of field data to anticipate equipment failures remains largely untapped.
This is precisely where AI shines, offering the ability to predict not just if, but when and why vital defense assets might fail. The military AI market is projected to reach a size of $35.54 billion by 2031, driven by AI’s ability to enhance decision-making, automation, and operational efficiency (Source: Military Embedded Systems).
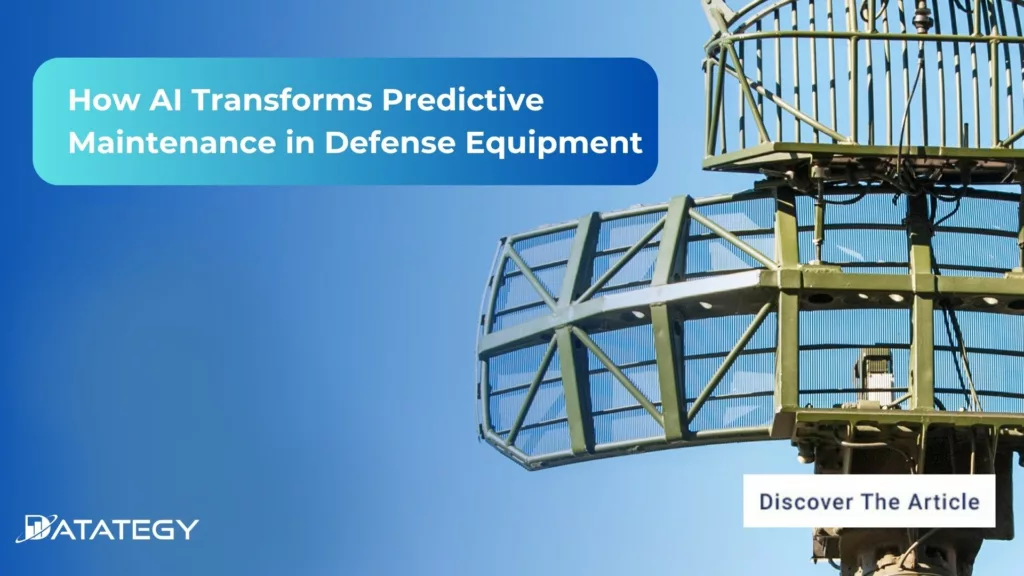
In this article, we’ll explore the benefits of AI in predictive maintenance, focusing on how it transforms operational efficiency and readiness.
The Evolution of Maintenance Technology in the Defense Sector
Maintenance in the defense sector was mostly a reactive paradigm in the 1980s. This required highly qualified workers to follow manual processes, depending on visual inspections, set timeframes, and a “repair-on-failure” strategy. Although strict for the period, this approach regularly caused unplanned operating outages for vital assets, including military ships, armoured vehicles, and aerial platforms.
The widespread adoption of computerised maintenance management systems (CMMS) in the 2000s marked a significant change. During this time, organised preventive maintenance programmes (PPM) and the early phases of condition-based monitoring (CBM) fueled a shift towards more proactive maintenance techniques. Simple sensors were added to equipment, gathering operational data like temperature or vibration that could be examined to spot possible irregularities before a major breakdown happened.
The technology environment for defense maintenance has changed significantly in recent years. These days, advanced predictive maintenance capabilities are powered by machine learning (ML) and artificial intelligence (AI). Advanced sensor suites on modern defense assets produce massive amounts of operational data in real time on performance, material deterioration, and environmental effects. This “big data” is processed by AI algorithms, which enable just-in-time maintenance interventions by precisely predicting when component failures are likely to occur.
What is Predictive Maintenance?
In order to predict when and why equipment is likely to break, predictive maintenance is a proactive strategy that makes use of data, sensors, and sophisticated analytics. In contrast to waiting for a breakdown or depending on planned maintenance, this approach continuously checks the state of machinery to identify wear, irregularities, or possible failures. To ensure that assets continue to function without needless downtime or expensive repairs, the objective is straightforward: address problems before they become serious. This strategy has proven crucial in industries like manufacturing, aviation, and defense.
Predictive maintenance has a direct impact on mission readiness and operational safety in the defense industry, going beyond time and cost savings. Aircraft, armoured vehicles, and naval systems are examples of military equipment that frequently function in harsh environments where failure is not an option. Defense companies can forecast problems, schedule maintenance precisely when it’s needed, and monitor performance in real time by utilising technology like artificial intelligence, machine learning, and Internet of Things sensors. This guarantees that vital assets are fully mission-capable whenever duty calls, in addition to extending their lifespan.
What are the Key Technologies Behind Predictive Maintenance Systems
1- Machine Learning
The foundation of defense predictive maintenance is machine learning (ML). Fundamentally, machine learning (ML) allows systems to learn from both past and current data in order to identify trends that can point to errors. For instance, ML models can identify minute changes in vibration, temperature, or sound that human operators might overlook when keeping an eye on a fighter jet’s engine. Over time, the algorithms become increasingly accurate by comparing normal operational behavior versus incidents that lead to mechanical difficulties.
The complexity of assets in the defense industry necessitates the use of advanced models that can process large datasets. These go beyond basic statistical models; they incorporate time-series forecasting that is tailored to each type of equipment, anomaly detection algorithms, and deep learning approaches. Importantly, machine learning (ML) correlates several data to determine “why” a component can fail as well as “when.”
This enables maintenance crews to take precise action, avoiding downtime without having to replace parts too soon. Additionally, as new data is added, machine learning (ML) keeps improving in accuracy, which is crucial in dynamic military settings where circumstances change quickly.
2- IoT Sensors
In order to collect the raw data required for AI-driven maintenance, the Internet of Things (IoT) is essential. IoT sensors are integrated into many vital defense equipment parts, including radar systems, hydraulics, engines, and even structural elements. These sensors give real-time insight into the condition of each system by continuously measuring variables including temperature, humidity, vibration, and pressure.
Predictive maintenance would not be possible without the Internet of Things. As machines’ sensory organs, sensors provide AI models with streams of data. IoT sensors, for example, can monitor engine performance in a variety of sea conditions or identify the degree of corrosion in hull components in naval vessels.
They monitor flight cycles, wing stress levels, and fuel system performance in aeroplanes. This continuous flow of data guarantees that AI systems have the most current and accurate image of the condition of the equipment, enabling more accurate forecasts and quicker interventions.
3- Edge Computing
Decisions in defense operations frequently need to be made quickly, particularly in contested or distant areas with poor connectivity. Instead of transmitting all data back to centralised data centres, edge computing handles this by processing data locally on the device or close to the source. This significantly lowers latency, allowing real-time predictive maintenance driven by AI.
Consider a war zone being flown over by an unmanned aerial vehicle (UAV). Without waiting for a remote server to assess the data, edge computing enables it to notify operators or take corrective action on its own if its AI model identifies unusual engine vibrations. In a similar vein, edge-based systems can continuously monitor vital components for navy boats operating far from shore, even in the absence of internet connectivity.
In addition to ensuring quicker reaction times, this local processing enhances data security, which is crucial for military operations. Cybersecurity and efficiency are enhanced by edge computing, which keeps critical data inside the operational environment.
What are the Benefits of Predictive Maintenance for Military Readiness
1- Reducing Downtime and Failure Risks
Downtime in military operations may harm national security, safety, and mission preparedness in addition to being an annoyance. Both reactive (repair it when it breaks) and scheduled (fix it at regular intervals) traditional maintenance strategies have obvious drawbacks. Either parts are changed too soon, squandering time and money, or the equipment breaks down abruptly, endangering the operation. This equation is drastically altered by AI-driven predictive maintenance, which continuously assesses the equipment’s state in real time to forecast when parts are likely to fail.
By identifying wear, weariness, or malfunction early on, this method reduces unplanned downtime. An AI system keeping an eye on an airplane’s engine, for instance, is able to identify minute variations in vibration or temperature that human specialists would miss. Maintenance teams can fix the problem after it has been identified before it becomes a serious malfunction that grounds the aircraft. All defense assets, including drones, radar systems, tanks, and submarines, can benefit from this predictive strategy.
By identifying problems before they become more serious, AI-based predictive maintenance can cut down on unplanned equipment stoppages by half. A 2024 Deloitte analysis, for instance, demonstrates a 50% decrease in unscheduled downtime across manufacturers.
2- Increasing the Lifespan of Equipment
Defense hardware is expensive and frequently has decades-long life cycles. The lifetime of armoured vehicles, missile systems, aircraft, and naval vessels depends on proper maintenance. Conventional maintenance methods can be conservative, replacing parts based on time-in-service measurements rather than actual wear. This can occasionally result in vital parts deteriorating undetected or underutilised assets being overmaintained.
Predictive maintenance powered by AI provides a more intelligent, data-driven approach. Instead of depending on strict deadlines, AI models evaluate the actual health of each component by continuously analyzing operational data. With this strategy, maintenance is only carried out when absolutely necessary, avoiding needless replacements and catastrophic failures.
Datategy experts estimate that predictive maintenance powered by AI extends the lifespan of defense equipment by an average of 27%. This life extension results from optimized usage, condition-based servicing, and early anomaly detection, preserving critical assets for longer operational cycles.
Predictive models might demonstrate that, depending on operational parameters like load or climate, certain oil pumps safely last 7,000 hours while others exhibit problems at 4,500. For instance, a naval engine’s oil pump is normally replaced every 5,000 hours.
3- Cost and Resource Allocation Efficiency
In order to balance the demands of advanced technology, operational preparedness, and long-term sustainability, military expenditures are constantly under strain. One large line item that frequently takes up a sizable amount of defense budgets is maintenance. Conventional maintenance approaches are inefficient because they either result in excessive expenditures for preventative measures or expensive fallout from unplanned malfunctions. By closely matching maintenance tasks with actual needs, predictive maintenance offers a more cost-effective strategy.
AI-driven predictive maintenance reduces defense operations costs by 30% on average, according to Datategy researchers. Lower maintenance costs, a smaller stock of spare parts, and more effective staffing allow defense companies to maximise resources without sacrificing preparedness.
Predictive maintenance maximises the use of workers. Defense operations frequently lack skilled technicians. By prioritizing which assets need repair and cutting down on time spent reviewing perfectly functional equipment, artificial intelligence (AI) helps allocate human resources more effectively. The efficiency of the supply chain is also increased since data-driven projections allow for the accurate ordering of tools and parts when needed rather than the “just in case” stockpiling of costly inventory.
What are the Applications in Defense Environments?
1- Ground Vehicles and Armored Equipment
Military operations on land rely heavily on ground vehicles, such as logistical trucks, tanks, and armoured personnel carriers (APCs). Extreme stress is frequently placed on these vehicles, including harsh weather, big cargoes, rugged terrain, and combat situations, all of which hasten wear and tear. In order to keep these assets combat-ready and lessen the logistical burden on support operations, predictive maintenance is essential.
This data is analysed by machine learning models to anticipate issues before they happen. For example, a slight increase in engine vibration under specific loads could be a sign of a piston problem. Because maintenance crews are notified well in advance, repairs can be made during scheduled downtimes as opposed to reactive, field-based situations.
It has a big effect. Missions go more smoothly, vehicles spend less time in repair depots, and fleet availability rises. Additionally, predictive maintenance minimises the demand for backup cars, maximising fleet size without compromising preparedness. Because crews can operate with the assurance that their equipment won’t malfunction in crucial situations, armoured vehicles are more effective in warfare.
2- Aircraft and Drone Fleet Maintenance
Scheduled intervals based on flight hours or cycles were a major component of maintenance in the past. Although this method was safe, it frequently resulted in the needless replacement of parts that were still in good shape or the failure to notice concealed flaws that surfaced in between inspections. By continuously evaluating data gathered from IoT sensors placed throughout the aircraft, AI radically alters this. These sensors provide real-time monitoring of engine temperatures, vibration levels, hydraulic pressures, fuel economy, and structural soundness.
Modern military and commercial aeroplanes are becoming flying data hubs; advanced predictive analysis is made possible by the 500 GB of sensor data produced by a single Boeing 787 flight (Source:defenseadvancement.com)
This enormous volume of data is then processed by machine learning models to find anomalies that might indicate possible failure or early wear. For example, a minor alteration in a jet turbine’s vibration pattern could be a sign of bearing deterioration, which would be invisible without AI-driven analysis. Predictive maintenance is especially important for UAVs since remote operators may only evaluate the drone’s health by using data feedback. AI guarantees that drones are safe to use on lengthy or dangerous missions in addition to being operational.
The advantages are obvious: preventive maintenance lowers unplanned mid-flight malfunctions, prolongs the life of costly parts, and increases fleet availability.
3- Naval Systems and Submarine Readiness
With integrated propulsion systems, weapon platforms, radar, sonar, and innumerable mechanical and electronic components, ships and submarines are effectively floating towns. The objective of the ship and the safety of the crew may be jeopardised by a malfunction in any of the vital subsystems, including the propulsion, cooling, or power-generating systems. Predictive maintenance powered by AI makes sure that these risks are reduced.
According to Datategy experts, AI-driven predictive maintenance improves naval and submarine readiness by an average of 25%
Data on factors including engine load, oil viscosity, hull integrity, corrosion levels, pressure in ballast tanks, and even acoustic signals that can indicate mechanical problems are continuously collected by a network of Internet of Things sensors positioned throughout the ship. Even in the face of changeable circumstances, like as choppy seas or extended missions, machine learning models use this data to forecast when components are likely to deteriorate or fail.
AI enables maintenance schedules to be more accurately based on usage and wear trends than on speculative estimations. Longer time at sea, more dependability, and fewer unplanned repairs are the outcomes of this.
What are the different Types of AI Models for Predictive Maintenance?
-
Time-Series Models:
Time-series models, such as ARIMA (AutoRegressive Integrated Moving Average) or LSTM (Long Short-Term Memory networks), process sequential data like temperature, vibration, or pressure readings from sensors. These models excel in identifying trends and forecasting when critical thresholds will be breached, signaling potential failures. -
Classification Models:
Classification algorithms, such as decision trees or random forests, categorize machinery states into “normal,” “at risk,” or “critical.” By learning from labeled data, these models help maintenance teams prioritize which machines need immediate attention, reducing the risk of unexpected breakdowns. -
Regression Models:
Regression models, including linear regression or neural networks, estimate the exact time-to-failure based on input variables. These models are particularly useful for continuous data, providing precise predictions that enable well-timed maintenance actions. - Survival Analysis Models:
In predictive maintenance, survival models analyze historical data to estimate the remaining useful life of machinery. These models calculate hazard rates (failure probabilities at specific times) and survival functions (the likelihood of continued operation over time), enabling proactive decision-making to minimize downtime and optimize equipment usage.
What does Survival Analysis Mean?
Survival analysis is a method developed in the fields of biology and medicine that looks at how long it will take for a certain event to occur, like the survival period of patients after treatment. Its main objective is to estimate the possible occurrence time of an event using historical data in order to understand and predict the chance of that event occurring over time.
What are the Key Principles of Survival Analysis?
1- Define the Event of Interest
Clearly defining the “event” under study is the first step towards applying survival analysis successfully. This is usually a failure in machinery, like a part failing, a system failing, or a piece of equipment stopping working. Accurately defining the event guarantees reliable and significant data gathering. For instance, think about whether a “failure” only refers to complete breakdowns or also includes partial malfunctions.
The integrity of the analysis depends on this clarity. Furthermore, by defining the event, the study’s objectives—like anticipating failures or enhancing maintenance plans—are in line with practical insights.
2- Analyze Time-to-Event Data
The main goal of survival analysis is to determine how long it takes for an event to occur. This could entail tracking the amount of time that passes between the beginning of operation and the first failure in machinery.
Time-to-event data provides information about how long a piece of equipment is dependable in typical circumstances. By going beyond averages, this method offers complex perspectives on durability and dependability. To guarantee high-quality insights from the analysis, precise time tracking and appropriate documentation of operational milestones are crucial.
3- Measure the Hazard Function
The hazard function focuses on the probability of failure at a specific moment in time, assuming the system has not yet failed. This dynamic statistic shows when there is a substantial chance of a machine breaking down. For example, an increase in risks at 1,000 hours of operation may indicate that a part needs to be changed. By monitoring hazard rates, failures can be prevented in advance.
What are the Benefits of Survival Analysis for Machine Maintenance
1- Increasing the Lifespan of Machines
Survival analysis assists in anticipating when machines are most likely to malfunction by examining the time-to-failure data and spotting trends that result in malfunctions. This realization makes it possible to take prompt action, like changing or adjusting components before they hit crucial failure points. Increasing a machine’s lifespan postpones the need for expensive replacements and saves money on repairs.
Additionally, it can guarantee that a business gets the most out of its equipment, which lowers the total amount of capital expenditure. Maintenance teams can make well-informed decisions to prolong a machine’s life by using the data-driven survival analysis approach, which gives them a precise understanding of the machine’s condition.
2- Saving Money on Maintenance
Survival analysis optimizes the timing of interventions, which lowers maintenance costs. Even when the machine is still operating properly, traditional maintenance techniques like time-based preventive maintenance frequently lead to needless part replacements or maintenance work. Businesses use survival analysis to transition from a scheduled or reactive approach to a predictive model in which maintenance is only carried out when required.
It lowers the frequency of expensive emergency repairs and prevents resource waste on unnecessary interventions by spotting early warning signs and anticipating failures. This focused strategy minimizes labor expenses and downtime by ensuring that parts are replaced at the most economical moment.
3- Reducing Downtime
survival analysis helps businesses plan maintenance tasks for planned breaks or off-peak hours, reducing downtime. Instead of waiting for an unplanned breakdown to interrupt operations, maintenance teams can replace or repair parts in advance when they know when a machine is likely to fail.
This proactive maintenance strategy guarantees seamless, continuous operations, boosts productivity, and reduces unscheduled downtime. In the end, survival analysis-driven predictive maintenance increases operational effectiveness and lessens the effect of interruptions on overall company performance.
4- Improved Compliance and Safety
Workplace safety is also influenced by real-time monitoring. Through constant monitoring of machinery and environmental factors, producers are able to identify risks before they endanger employees. Furthermore, data analysis lowers the danger of legal or regulatory problems by ensuring that activities meet necessary standards and maintaining compliance with safety rules.
What are the Common Challenges in Applying Survival Analysis in Real-World Applications?
1- Ensuring Data Quality and Accuracy
Assuring complete and high-quality data is one of the biggest obstacles to using survival analysis for actual machine maintenance. Historical performance information, including machine usage, failure incidents, and maintenance logs, is crucial to survival analysis. Incomplete, erroneous, or inconsistent data can greatly distort the analysis’s findings and produce incorrect predictions. In real-world applications, equipment may run in a variety of settings with varying conditions, and not all maintenance procedures or failures may be accurately recorded.
2- Integration with Existing Systems
Integrating survival analysis with current machine monitoring and maintenance systems presents another difficulty. Predictive maintenance platforms, asset management software, and enterprise resource planning (ERP) systems are already used by many businesses. The intricate statistical models needed for survival analysis may be too much for these systems to handle. It can be challenging and resource-intensive to integrate survival analysis models into these current workflows, necessitating a high level of technical expertise
3) Resistance to Adoption and Change
Organizational resistance may result from survival analysis’s departure from conventional maintenance procedures. Many maintenance teams are used to reactive repairs or time-based, scheduled maintenance. A cultural and operational change is necessary to implement survival analysis, and stakeholders must accept and trust data-driven decision-making. This entails overcoming reluctance to adopt new technologies and altering ingrained maintenance practices for a lot of businesses.
Datategy Magazine: AI Industrialization & Future Challenges
Datategy Magazine serves as your premier source for in-depth data insights, offering comprehensive coverage of the latest trends, strategies, and developments in the data industry. With a focus on AI industrialization and future challenges, we provide valuable analysis and expert commentary to help you stay ahead in this rapidly evolving landscape.
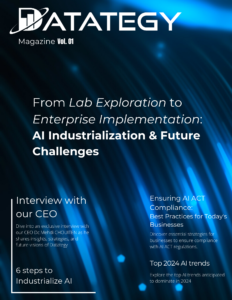
Use Case: How papAI Enhance Failure Prevention and Machine Lifetime Forecasting
1- Data Import and Integration
Raw Data Collection
Every predictive maintenance journey begins with data. Sensor data from machines, often stored in databases, forms the backbone of the analysis.
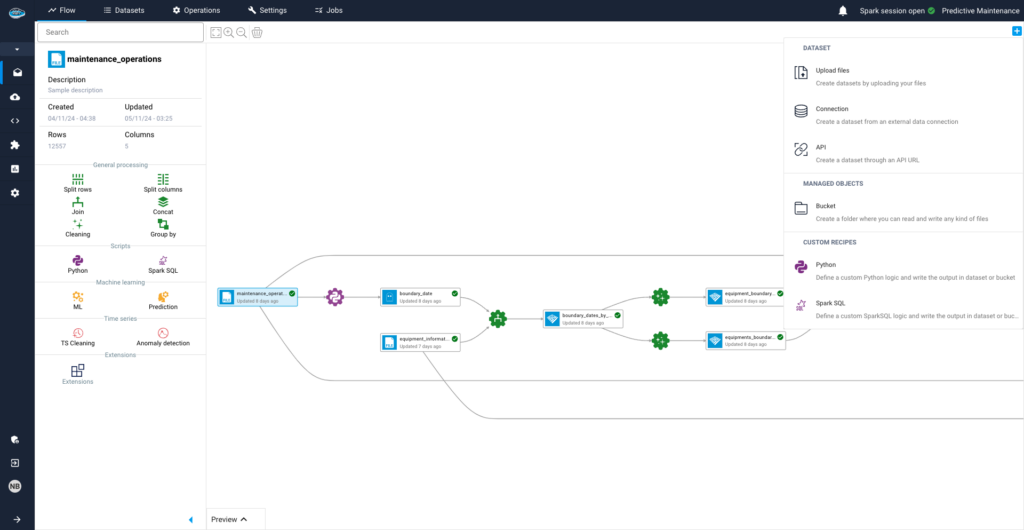
Seamless Connectivity with papAI
papAI’s integrated connectors simplify the data import process. In just a few clicks, raw data is imported, automatically processed, and ready for analysis, eliminating time-consuming manual configurations.
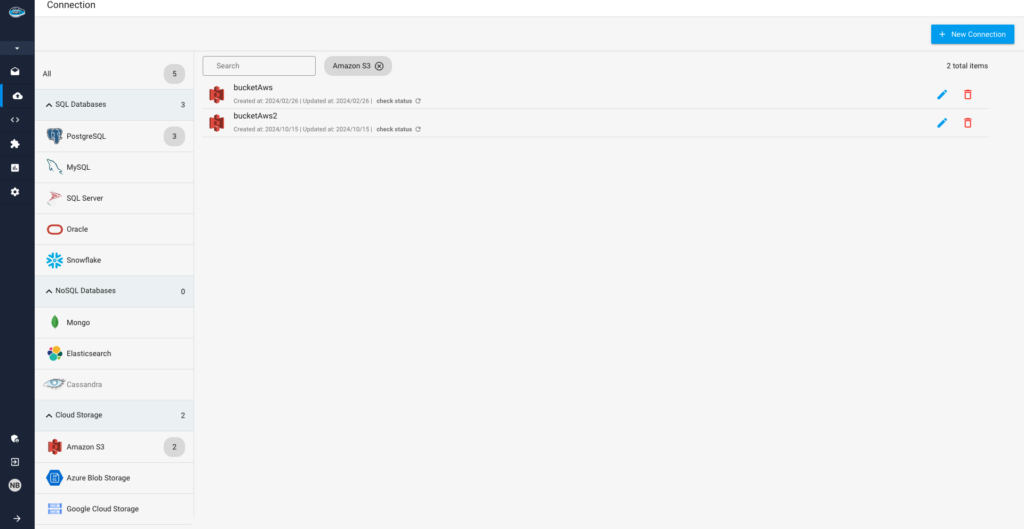
2- Data Cleansing: The Foundation of Accurate Models
Raw data is rarely perfect. It often contains missing values, errors, or anomalies that can degrade model performance. Proper data cleansing ensures models are accurate and unbiased.
Data Cleansing: The Foundation of Accurate Models
- Join Operations: Combine datasets from various sources seamlessly, regardless of their original structure.
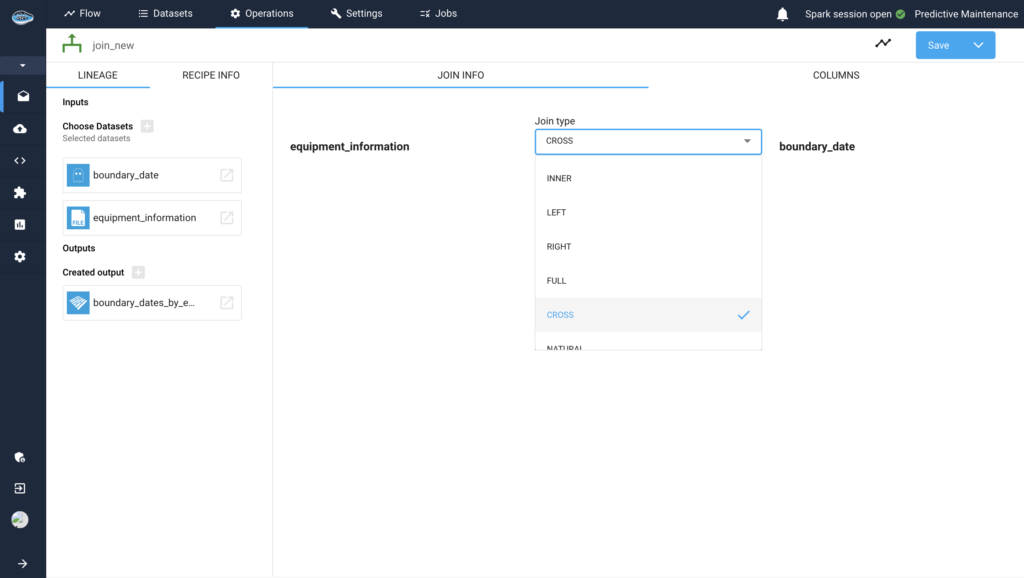
- Scripting Capabilities: Use Python or SparkSQL for custom data transformations. For instance, a SparkSQL recipe in papAI generates a comprehensive list of maintenance events, helping isolate critical data.
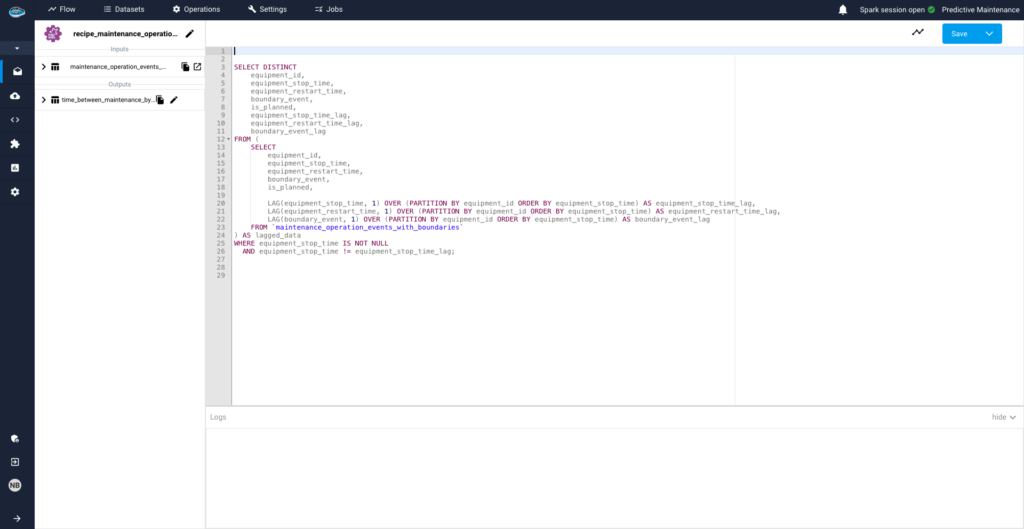
- Targeted Cleaning: With papAI’s Formula Edition, unexpected downtimes can be isolated by excluding planned maintenance. This defines precise targets for survival analysis.
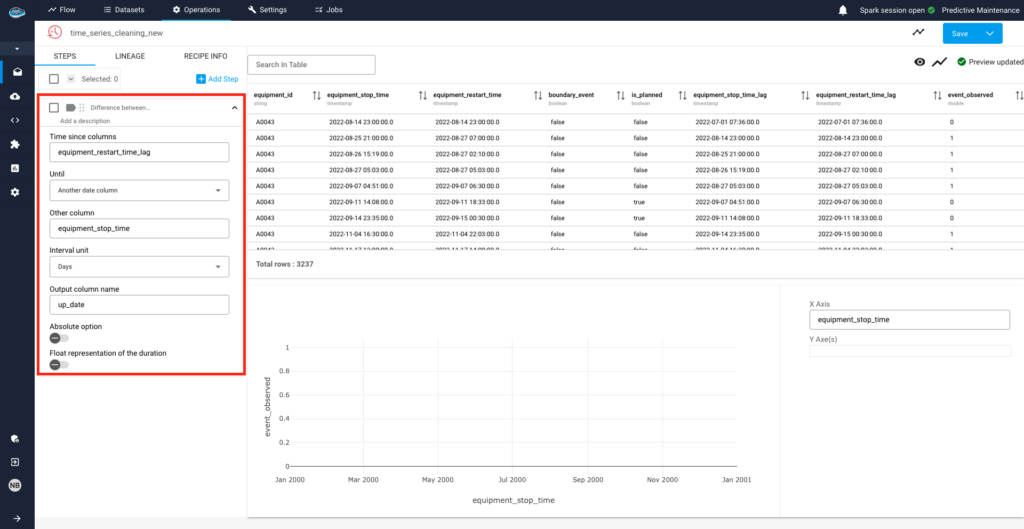
- Time Series Cleaning: By including the “up_date” variable, which tracks machine operation since the last maintenance, papAI enhances survival model predictions of remaining operational time.
3- Extending the Experience: Interactive Applications
- From Scripts to User-Friendly Applications
papAI transforms complex maintenance scripts into interactive dashboards, tailored to specific projects. These dashboards offer easy access to insights for all team members.
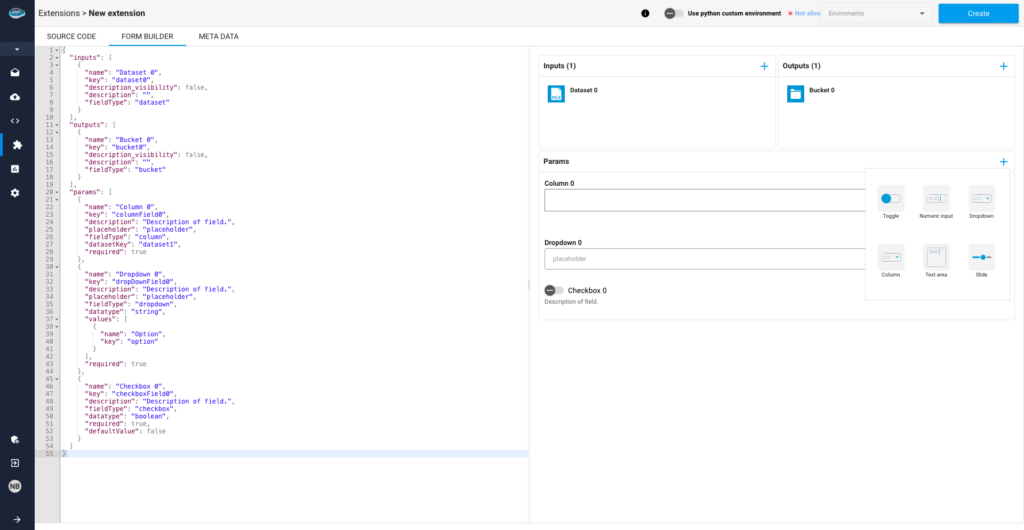
- Automation and Accessibility
Collaborators can share these tools, ensuring automated workflows and streamlined decision-making.
4- Survival Analysis for Machine Life Prediction
- The Survival Model Explained
Survival models estimate the likelihood of a machine’s operation over time. By leveraging historical data, these models predict the remaining life of equipment and assess failure risks.
- Predictive Maintenance in Action
Combining sensor data (e.g., vibration, temperature) with survival models, papAI calculates the probability of machine failure over varying timeframes. This enables maintenance managers to identify at-risk machines and prioritize interventions.
- Kaplan-Meier Chart
Visualize machine survival probabilities with a Kaplan-Meier chart. This intuitive tool highlights critical periods when machines are more prone to failure.
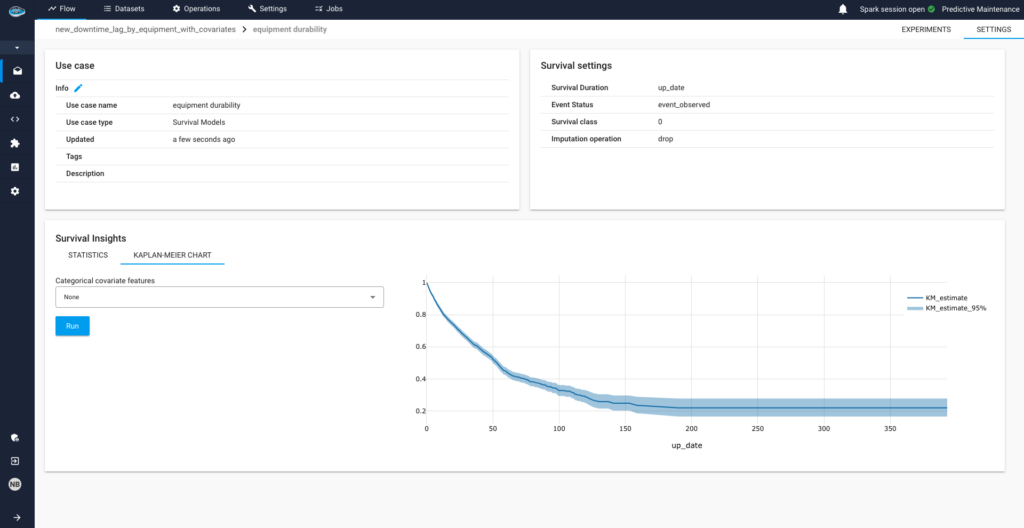
- Characteristic Coefficients
Survival models in papAI include coefficients that reveal the impact of variables like vibration or temperature. As new data is collected, these coefficients are refined, continuously improving model accuracy.
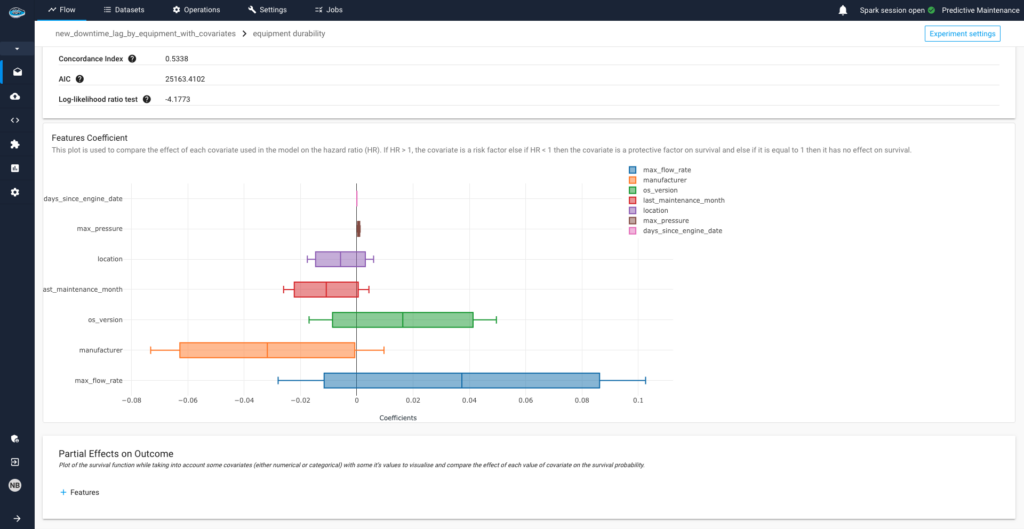
Classification of Threshold Events: Preemptive Warning Signals
- Understanding Threshold Events
Sensor-detected anomalies, or threshold events, indicate machines operating at their safety limits. These events are early warning signs of potential failures.
- Event Classification and Response
papAI uses classification algorithms to categorize these events by criticality. Maintenance teams can then prioritize responses, focusing on high-risk machines while monitoring minor anomalies.
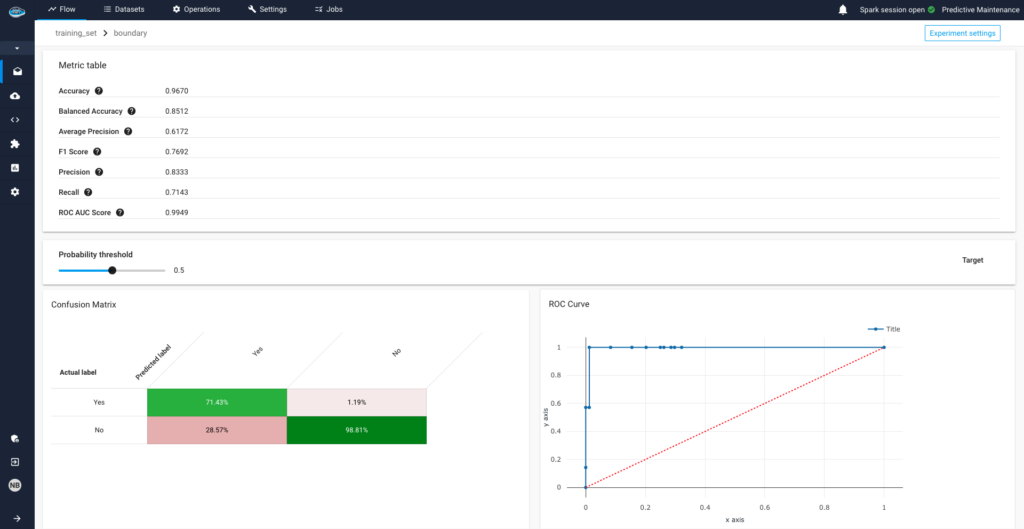
- Explainability and Counterfactuals
papAI’s explainability features (e.g., SHAP values) reveal why an event is critical, increasing team confidence. Counterfactuals simulate alternative scenarios, showing how changes in conditions (like reduced vibration) might lower failure risk. This helps teams take targeted corrective actions.
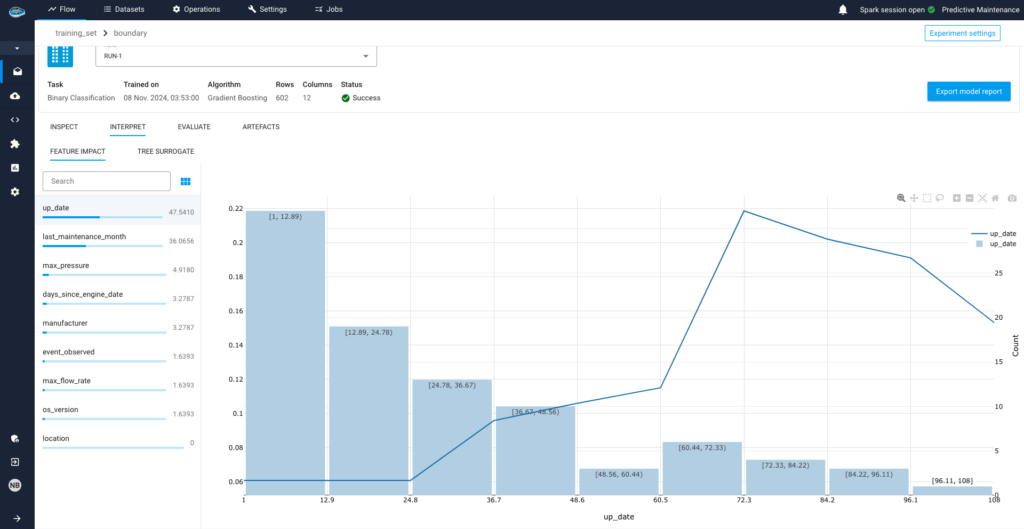
Create Your Own Failure Prevention Model using papAI solution
Traditional maintenance relies on fixed schedules or reactive repairs after failures occur. AI-powered predictive maintenance uses real-time data from sensors combined with machine learning to predict failures before they happen. This approach optimizes maintenance schedules based on actual equipment condition rather than generic timelines, reducing downtime, extending asset lifespan, and improving mission readiness
According to Datategy experts, benefits include up to 45% reduction in unplanned downtime, 27% increase in equipment lifespan, 25% improvement in operational safety, and 30% reduction in maintenance costs. These advantages lead directly to enhanced fleet readiness, lower operational risks, and significant cost savings across air, sea, land, and cyber-physical defense systems.
Aircraft and drones, improving MTBF and mission readiness.
Naval ships and submarines, reducing unexpected failures at sea.
Ground vehicles and armored fleets, lowering breakdown risks in tough terrains.
Cyber-physical systems, like radar networks and missile defenses, by preventing both mechanical and digital failures.
IoT sensors that collect real-time data from equipment.
Machine Learning models that analyze patterns to predict failures.
Data fusion technologies that combine information from multiple sources for more accurate diagnostics.
Edge computing, enabling real-time decision-making in remote or constrained environments.
Digital twins, offering virtual simulations of assets to test scenarios and predict degradation.
Interested in discovering papAI?
Our AI expert team is at your disposal for any questions
How to Orchestrate AI Deployment in Defense Infrastructures?
How to Orchestrate AI Deployment in Defense Infrastructures? The need...
Read MoreHow AI-Powered Anti-Drone Solutions Transform Defense Operations?
How AI-Powered Anti-Drone Solutions Transform Defense Operations? Drones are everywhere...
Read MoreTransform Defense Logs & Rapport into Situational Awareness with AI
Transform Defense Logs & Rapport into Situational Awareness with AI...
Read More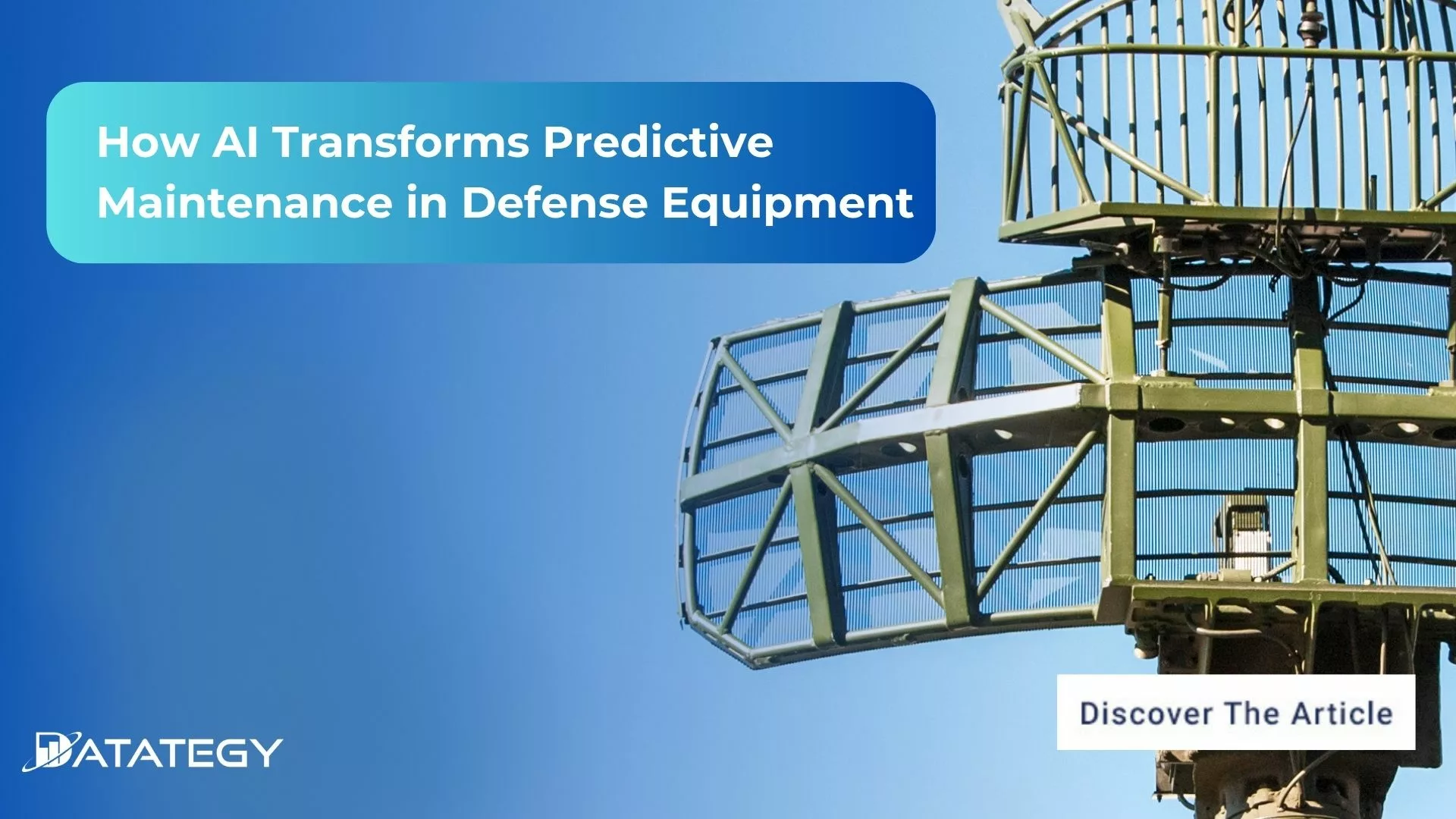
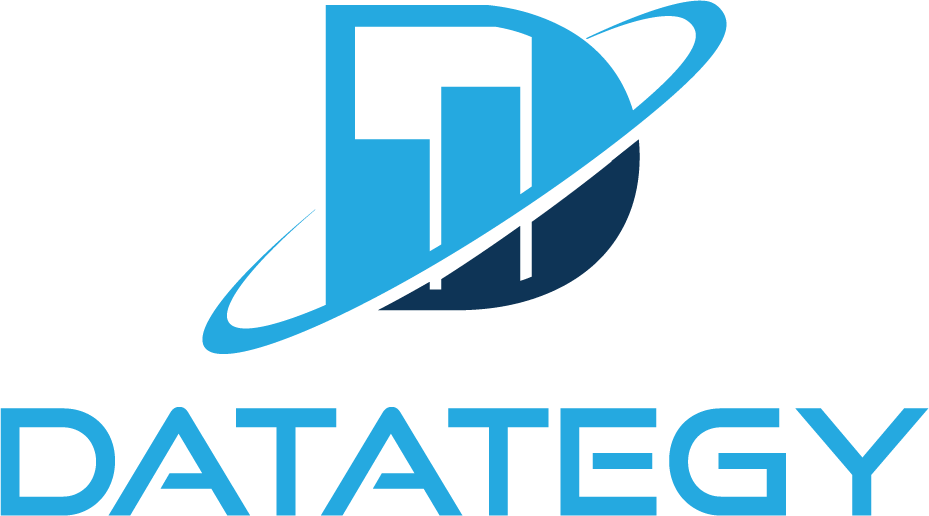