Transform Defense Logs & Rapport into Situational Awareness with AI...
Read MorePredictive vs Preventive Maintenance: What is AI’s Role?
Table of Contents
ToggleMaintenance is the lifeblood of any operation, ensuring the smooth running of machinery and systems. Without proper maintenance, equipment can break down, leading to costly downtime, reduced productivity, and potential safety hazards.
Preventive maintenance and predictive maintenance are the two main maintenance approaches that stand out. Predictive maintenance uses cutting-edge technologies, such as artificial intelligence (AI), to foresee possible failures before they happen, whereas preventive maintenance entails planned inspections and repairs. Predictive maintenance increases asset lifespan, optimizes resource allocation, and reduces downtime by proactively addressing problems.
Find out how papAI can improve the deployment of AI projects in the Manufacturing Industry.
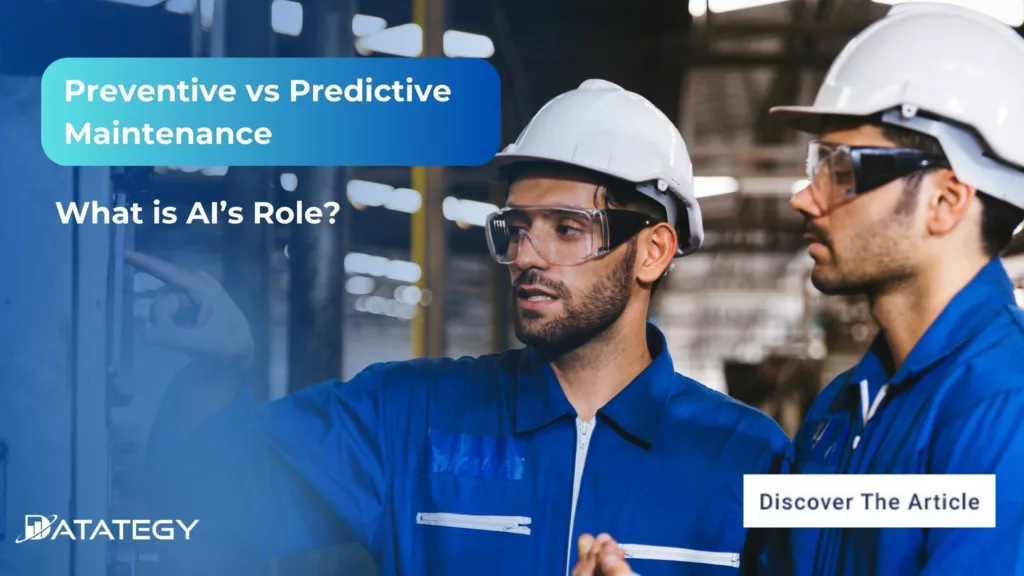
In this post, we explore how artificial intelligence (AI) is transforming maintenance practices and enabling new levels of efficiency.
What Does Preventive Maintenance Mean?
Preventive maintenance helps maintain optimal performance by proactively addressing possible problems before they arise, which helps to minimize disruption and facilitate smoother operations. For businesses looking to minimize the likelihood of unplanned breakdowns while maintaining their assets in optimal condition over time, this approach is crucial.
Preventive maintenance is fundamentally about routine care based on usage patterns or time intervals, as opposed to responding to issues after they arise. Teams are able to anticipate wear and tear, make the required repairs, and swap out parts before they break down thanks to this proactive approach. The objective is to decrease the overall cost of maintenance, increase efficiency, and prolong the life of systems and equipment. Comprehending this strategy entails recognizing the harmony between maximizing asset value and reducing downtime.
What are the Benefits of Preventive Maintenance?
Extended Equipment Lifespan: By addressing wear and tear before it becomes a significant problem, preventive maintenance helps keep machinery and equipment in top condition. Frequent maintenance increases asset longevity, minimizing the need for premature replacements and optimizing investment.
Decreased Unexpected Downtime: Companies can avoid costly downtime caused by unexpected failures by planning maintenance and inspections. This proactive strategy keeps productivity high by ensuring that operations continue without significant disruptions.
Savings: Preventive maintenance is cost-effective over time, despite the initial expenses. It lessens the impact of equipment failure and the need for costly emergency repairs, saving money on repairs as well as possible lost revenue from downtime.
Increased Safety: Equipment that receives routine maintenance runs more dependably and safely, reducing the possibility of mishaps brought on by broken machinery. Preventive maintenance guarantees that safety regulations are followed and that there are no preventable risks at work.
Increased Efficiency: Equipment that has received regular maintenance operates more effectively, which can result in better performance and lower energy costs. By minimizing waste or needless consumption and enabling systems to operate at their peak efficiency, preventive maintenance helps maximise operational output.
The Key Technology Behind Preventive Maintenance using AI
Data Collection
AI-driven preventive maintenance is built on data collection, which allows for precise decision-making based on real-time insights. IoT (Internet of Things) sensors, which continuously monitor a variety of parameters like temperature, vibration, pressure, and load, are frequently found in modern machinery and equipment. Data from these sensors is sent to a centralised system for processing, analysis, and storage.
In order to make sense of this enormous amount of data, AI algorithms filter and arrange it. Making sure that sensors are positioned strategically to gather all pertinent operational data without flooding the system with extraneous information is essential to efficient data collection. Basic operational metrics as well as environmental elements that impact equipment performance, such as humidity and outside pressures, can be included in the data gathered in this manner.
Predictive Analytics
A potent application of artificial intelligence (AI) in preventive maintenance is predictive analytics, which uses both historical and current data to predict when equipment is likely to break down or need maintenance. Large datasets from equipment history, such as maintenance logs, operational performance data, and failure records, are used to train machine learning algorithms at the start of the process. These algorithms examine relationships and patterns in the data to make remarkably accurate predictions about the future. Predictive maintenance models, for example, can spot subtle, slow changes in equipment behaviour that could point to an impending failure.
Automated Surveillance
The key to AI’s success in preventive maintenance is automated monitoring, which provides ongoing equipment supervision without necessitating constant human involvement. The sensors on the equipment are integrated with AI systems to provide real-time performance monitoring. Autonomously gathering, analysing, and interpreting data, these systems notify maintenance teams of possible problems. Temperature, vibration levels, and fluid pressure are just a few of the variables that the AI can monitor at once and determine if they fall within typical operating ranges. The system can automatically create work orders for maintenance teams or sound an alert when it detects deviations from the expected parameters.
IoT integration
By linking machines, sensors, and devices throughout the entire operation, the combination of AI and IoT technology makes preventive maintenance smarter and more effective. Large volumes of data are gathered by IoT devices from a variety of sources, including production lines, environmental sensors, and machinery. AI systems use this data as input, analysing it to produce useful insights about operational and equipment health. Businesses can get a comprehensive picture of their assets by fusing AI and IoT, which enhances maintenance plans and decision-making. IoT sensors, for example, monitor changes in equipment behavior in real-time and feed this data to AI models, which can then forecast probable failures or recommend performance enhancements.
What Does Predictive Maintenance Mean?
In order to comprehend predictive maintenance, one must acknowledge that it is a progressive method of equipment maintenance that employs technology and data to anticipate possible failures before they occur. Predictive maintenance, in contrast to traditional maintenance techniques, focusses on real-time equipment performance monitoring and analysis, allowing teams to take precise action when necessary.
Through the use of sensors, data analytics, and artificial intelligence, this approach detects minute alterations in equipment that indicate wear or inefficiency, enabling prompt maintenance. In addition to preventing unplanned malfunctions, this proactive strategy makes sure that maintenance is only carried out when absolutely required, saving time and money.
Fundamentally, predictive maintenance aims to strike a balance between reducing equipment downtime and increasing its lifespan. It moves the emphasis to a need-based, data-driven model from regular, schedule-based maintenance. Businesses are able to foresee issues rather than respond to them by using predictive maintenance to examine trends and patterns in the way equipment functions.
What are the Benefits of Predictive Maintenance?
Decreased Downtime: Predictive maintenance detects possible problems before they become serious, reducing unscheduled equipment failures. This proactive strategy guarantees that equipment is maintained at the appropriate time, greatly minimizing unplanned downtime and maintaining seamless operations.
Financial Savings: Predictive maintenance helps prevent damage to other components and costly emergency repairs by addressing issues early. Additionally, it minimizes needless maintenance, which optimizes expenses and prolongs the equipment’s lifespan, ultimately saving money.
Increased Reliability of Equipment: Equipment operates at its peak efficiency thanks to ongoing monitoring and data analysis. By identifying even small inefficiencies, predictive maintenance enables prompt adjustments to keep equipment running dependably and effectively, increasing overall productivity.
Data-Driven Decision Making: Maintenance teams can decide when and how to service equipment with the help of real-time data and predictive insights. Long-term operational efficiency is increased as a result of improved planning, resource allocation, and overall maintenance strategy.
The Key Technology Behind Predictive Maintenance using AI
Predictive Algorithms
Predictive algorithms are used by AI to examine data gathered from machinery. By processing both historical and real-time data, these algorithms use statistical models and machine learning to find patterns and trends that may indicate equipment failures. The subtle indications of wear or inefficiency that human operators might miss are picked up on by predictive algorithms. A progressive rise in temperature or vibration, for instance, could be a sign of an impending machine component failure. Predictive algorithms assist maintenance teams in scheduling timely interventions by predicting when a failure is likely to occur. This avoids costly downtime and guarantees that resources are used effectively.
Monitoring in Real Time
A key component of AI-powered predictive maintenance is real-time monitoring. Critical parameters, including temperature, pressure, vibration, and operating speed, are continuously monitored by sensors integrated into machinery. Artificial intelligence systems receive data from these sensors instantaneously, analyze it in real-time, and look for even the smallest irregularities.
Organisations can see the health of their equipment in real-time thanks to this instant feedback, which enables them to spot possible problems early on. Real-time monitoring has the advantage of serving as a preventive safety net, warning maintenance teams of minor malfunctions or inefficiencies before they become serious issues. AI-powered monitoring guarantees optimal operational performance and lowers the risk of unplanned downtime by providing ongoing oversight.
Automated Notifications
Critical maintenance issues are promptly addressed thanks to automated alerts. AI-powered systems analyze data continuously and send out alerts when anomalies or possible malfunctions are found. Maintenance teams are able to take prompt action before issues worsen thanks to these real-time alerts. By reducing the need for manual monitoring, automated alerts save time and guarantee a quicker reaction to possible threats. To reduce the chance of equipment damage, the AI system might, for example, instantly notify the appropriate staff if a machine’s temperature rises above acceptable bounds. Workflows are streamlined and maintenance tasks are efficiently prioritized thanks to this automated communication.
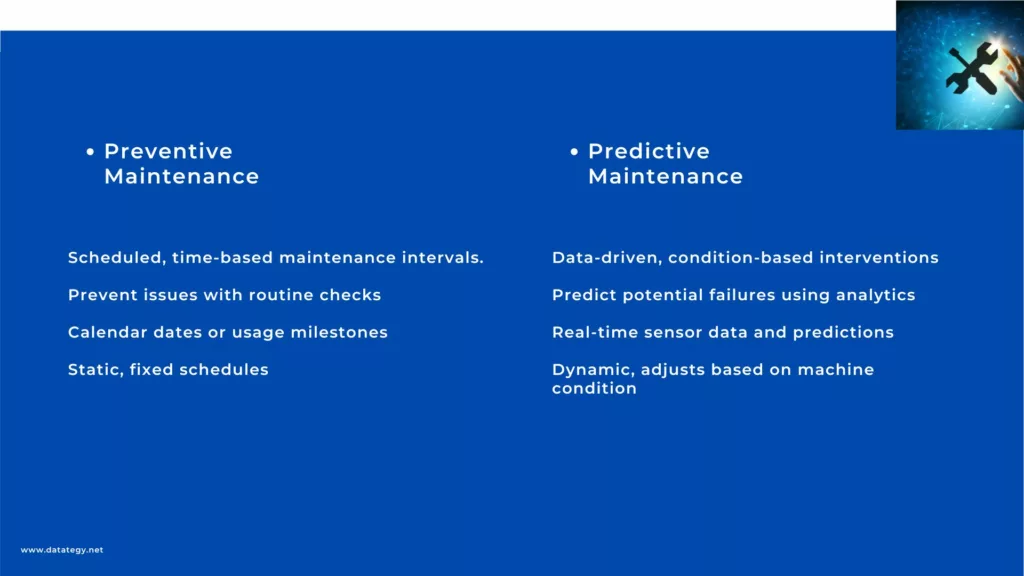
When to Use Preventive or Predictive Maintenance?
Depending on your equipment type, operational objectives, and available resources, you must choose between predictive and preventive maintenance. Simpler systems or equipment with predictable wear patterns are the ideal candidates for preventive maintenance. To lower the chance of unplanned malfunctions, it depends on planned maintenance that is based on time intervals or usage milestones.
Preventive maintenance is a dependable strategy that guarantees regular inspections and replacements to keep equipment operating efficiently if your company values consistency and uncomplicated planning. This approach is especially effective for assets with easily manageable downtime or minimal failure consequences.
On the other hand, predictive maintenance is best suited for expensive, sophisticated equipment where unscheduled downtime would have a major effect on operations or finances. Predictive maintenance identifies the likelihood of specific component failures and enables prompt interventions by utilizing cutting-edge technologies such as artificial intelligence (AI), the Internet of Things (IoT), and real-time data analytics. Because it bases maintenance efforts on real needs rather than preset schedules, this method is incredibly effective.
What Challenges need to be Overcome before Implementing Real-Time Monitoring and Data Analysis Platform?
Costs and ROI: The initial investment required for new technologies is a significant barrier, particularly for small and medium-sized businesses. It can be intimidating to invest in sensors, data integration tools, and AI-powered systems. Organizations must, however, consider these expenditures as long-term investments that eventually lower costs and improve operational efficiency. To overcome this obstacle, a comprehensive cost-benefit analysis must be carried out, and stakeholders’ support must be gained by showcasing the potential return on investment and competitive advantages.
Ensuring Data Quality for Reliability: Implementing cutting-edge technologies like predictive maintenance presents additional challenges related to data management and quality. Data that is inconsistent, lacking, or erroneous can compromise the efficacy of machine learning and artificial intelligence models. To guarantee accuracy, businesses must set up strong procedures for data collection, storage, and analysis. Reliability can be increased by using sophisticated analytics tools and routinely auditing data inputs. Organisations can overcome implementation obstacles and unlock the full potential of their new systems while guaranteeing long-term success by concentrating on these fundamental elements.
How to choose the best AI solution for your data project?
In this white paper, we provide an overview of AI solutions on the market. We give you concrete guidelines to choose the solution that reinforces the collaboration between your teams.
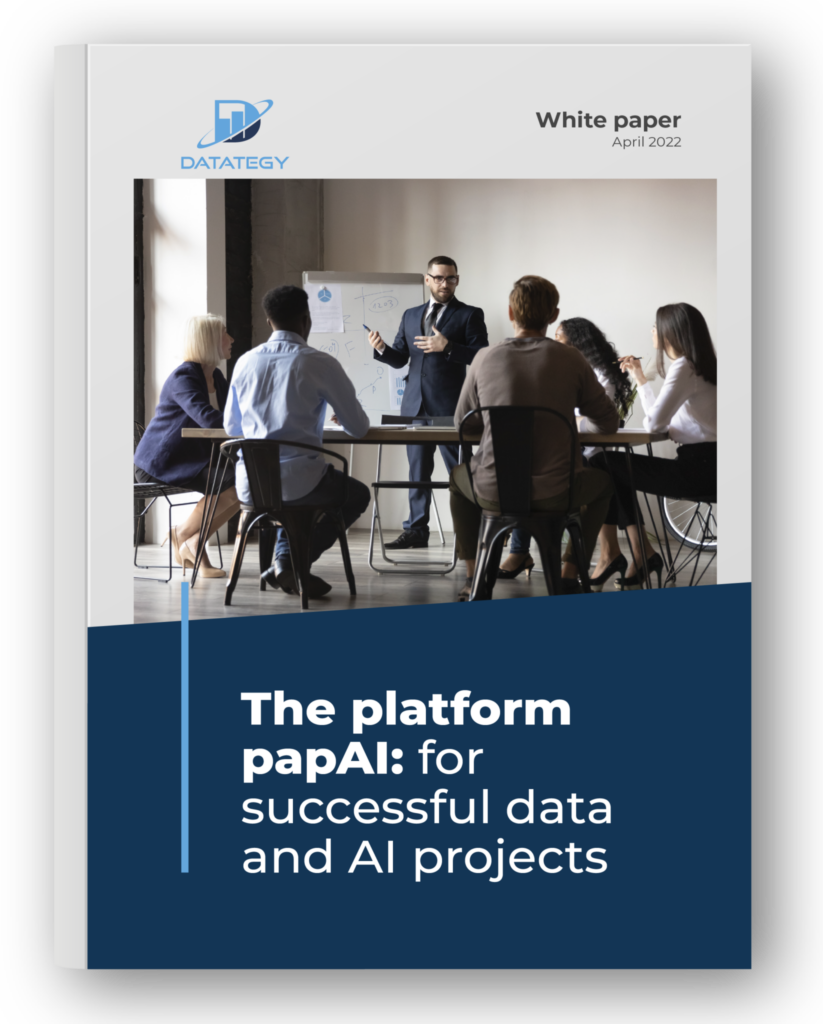
How papAI Helps Build Effective Preventive and Predictive AI Models?
papAI is an All-in-One AI solution made to optimize and simplify processes in a variety of sectors. It offers strong capabilities for data analysis, predictive insights, and process automation by fusing state-of-the-art artificial intelligence and machine learning technology.
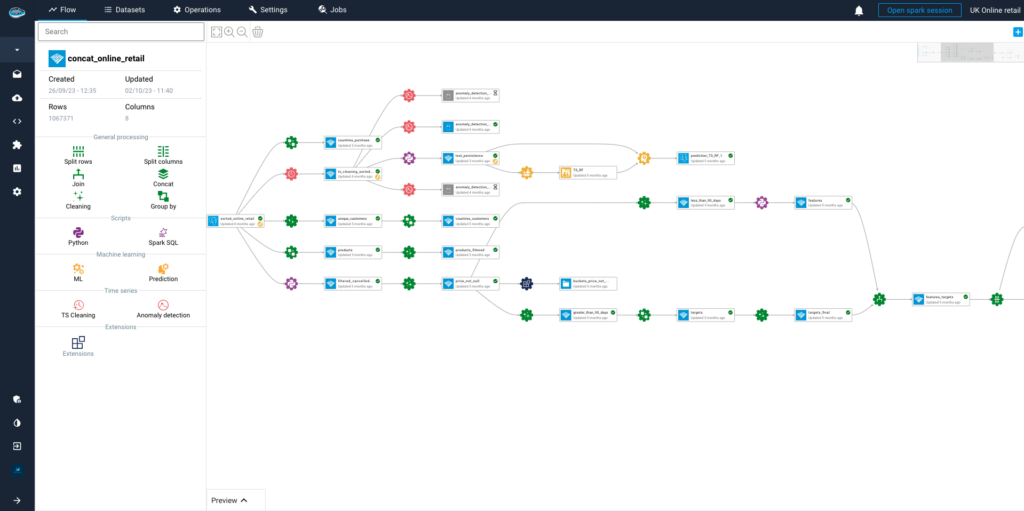
Here’s an in-depth look at the key features and advantages of this innovative solution:
Create Custom AI Models for Maintenance
By enabling businesses to develop customized AI models for predictive and preventive maintenance, papAI guarantees that the solutions meet their particular operational requirements. PapAI collects data from various sources, such as IoT sensors, historical documents, and environmental conditions, by seamlessly integrating with current systems.
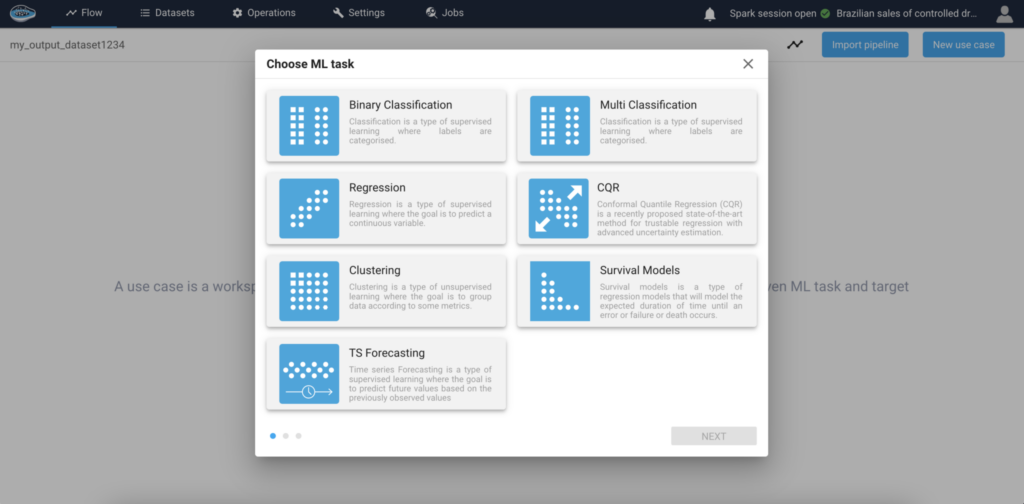
Data Integration and Centralization
Gathering and consolidating data from various sources is one of the first steps papAI takes in creating predictive and preventive maintenance models that work. This comprises information from historical maintenance records, environmental variables, machinery logs, and Internet of Things sensors. PapAI guarantees that all pertinent data is consistent and easily accessible by combining these data points into a single platform. This thorough perspective enables businesses to gain a better understanding of how their equipment functions in various scenarios, which is crucial for developing models that accurately represent performance in the real world.
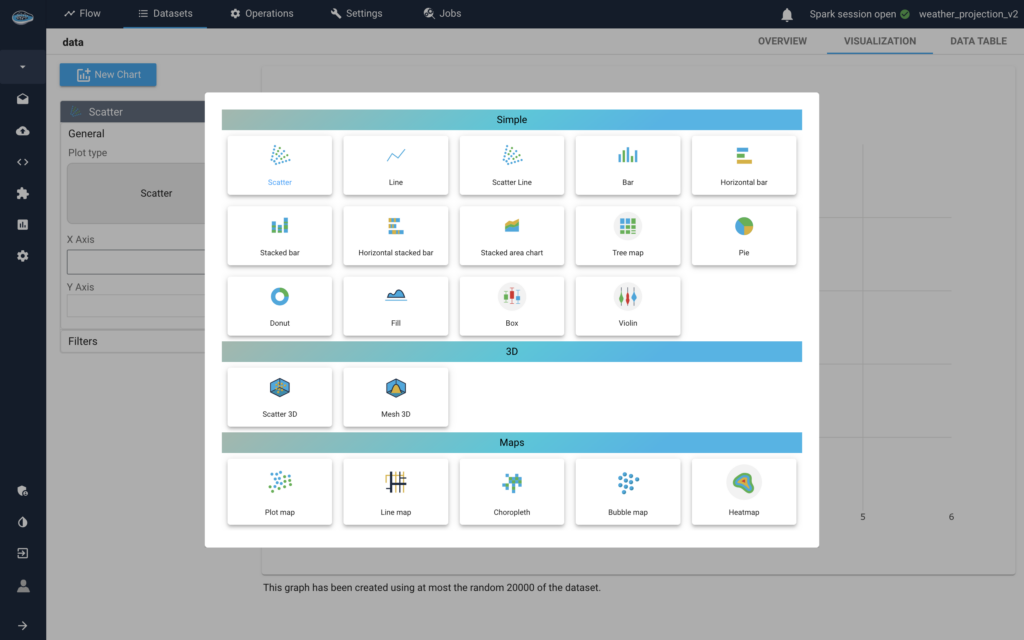
Predictive Analytics and Failure Forecasting
papAI uses predictive analytics to anticipate equipment failures before they happen after the data is combined and the models are tailored. Its machine learning models continuously examine real-time data to spot minute variations in performance that might point to possible problems. This capability enables papAI to offer early warnings for predictive maintenance, enabling teams to take preventative measures instead of waiting for an unplanned malfunction. This enhances overall equipment reliability while lowering unscheduled downtime and expensive repairs. In addition to preventing malfunctions, papAI enables companies to maximize their resources and reduce downtime by precisely forecasting when maintenance is required.
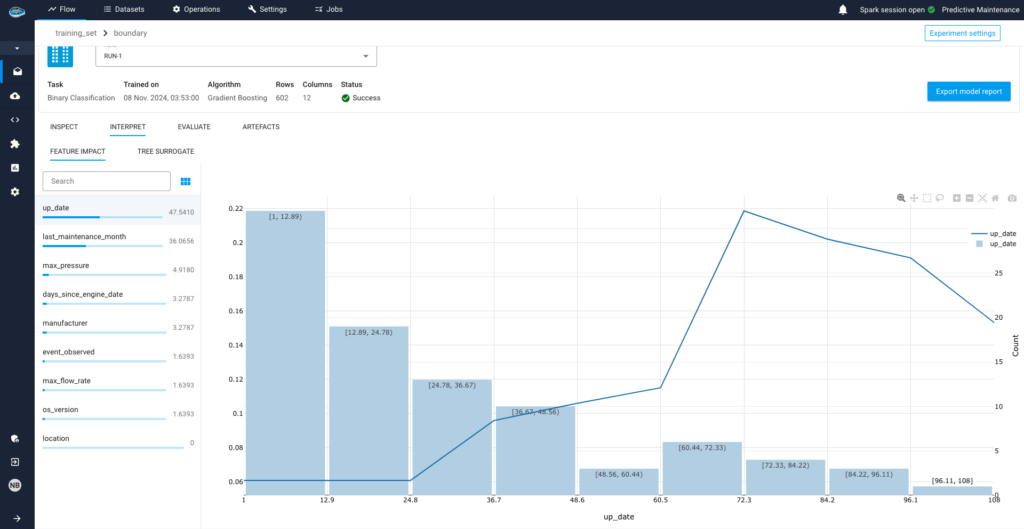
Create your Own Preventive or Predictive Maintenance Model using papAI solution
To sum up, papAI gives companies the freedom and resources to design unique predictive and preventive maintenance models that are suited to their particular operational requirements. Through the use of cutting-edge AI, real-time monitoring, and predictive analytics, papAI helps businesses to increase equipment lifespans, lower maintenance costs, and minimize downtime. Every decision is founded on actionable insights thanks to its capacity to integrate and analyze enormous volumes of data, which maximises performance and boosts overall efficiency.
Schedule a demo with us right now to see how papAI can revolutionize your equipment management if you’re prepared to advance your maintenance plan. Together, we can create a more intelligent future for your company.
Preventive maintenance involves scheduled inspections and repairs based on time intervals or usage patterns, while predictive maintenance uses AI and real-time data to predict failures before they happen, allowing for more targeted intervention.
AI improves preventive maintenance by analyzing large volumes of data from IoT sensors and historical performance, helping businesses predict when maintenance is needed and automate monitoring, leading to less downtime and more efficient operations.
- The main technologies include predictive algorithms that process data to predict failures, real-time monitoring through sensors that track equipment performance, and automated notifications that alert teams to potential issues, improving efficiency and reducing downtime.
- Preventive maintenance is ideal for simpler systems or equipment with predictable wear patterns, where routine checks can keep operations running smoothly. Predictive maintenance is better suited for complex, high-value equipment where unplanned downtime would significantly affect operations or revenue.
Interested in discovering papAI?
Our AI expert team is at your disposal for any questions
Why AIOps Is Key to Cyber Threat Detection in Defense?
Why AIOps Is Key to Cyber Threat Detection in Defense?...
Read MoreHow AI Transforms Predictive Maintenance in Defense Equipment
How AI Transforms Predictive Maintenance in Defense Equipment In a...
Read MoreHow to Scale AI Without Breaking Your Infrastructure in 2025
How to Scale AI Without Breaking Your Infrastructure in 2025...
Read More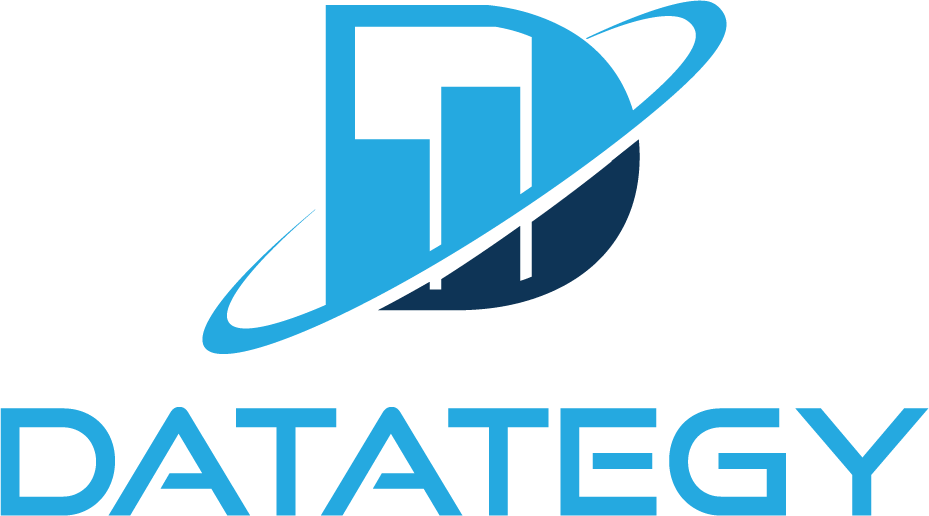